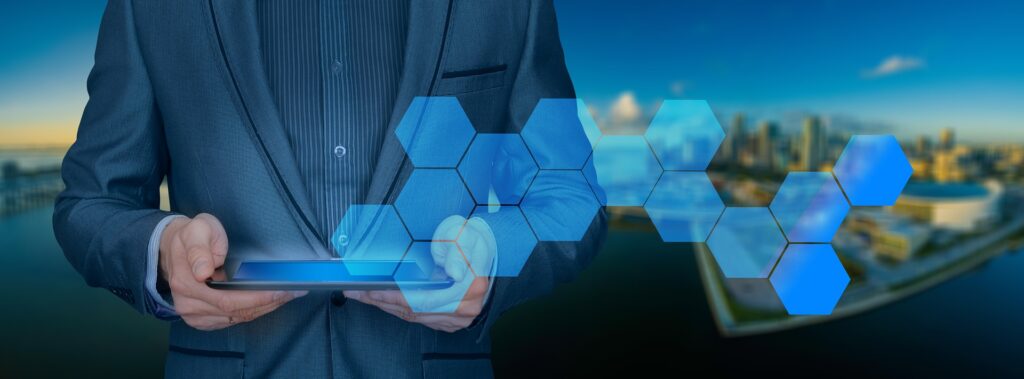
APS and MRP
Probably this post should have been one of the first of this blog, but it’s not too late. Derek Singleton pointed me
his article about the differences between APS and
MRP systems and after reading it I can say that I largely agree with him about the differences between the two types of systems by the point
of view of the business environments where they can be used more profitably. His article has been an occasion for me to look for a good definition
of APS, to better communicate the usefulness and role of these kind of systems. The definition in the APICS dictionary doesn’t help too much in narrowing the concept:
“Techniques that deal with analysis and planning of logistics and manufacturing
during short, intermediate, and long-term time periods. APS describes any computer
program that uses advanced mathematical algorithms or logic to perform
optimization or simulation on finite capacity scheduling, sourcing, capital planning,
resource planning, forecasting, demand management, and others. These techniques
simultaneously consider a range of constraints and business rules to provide real-time
planning and scheduling, decision support, available-to-promise, and capable-to-promise
capabilities. APS often generates and evaluates multiple scenarios.
Management then selects one scenario to use as the ‘official plan’. The five main
components of APS systems are (1) demand planning, (2) production planning, (3)
production scheduling, (4) distribution planning, and (5) transportation planning.”
This definition is mostly based on what aps do (listing of modules) and less on how they do it. The most of commercial packages usually
considered APS don’t cover the complete range of
modules provided by APICS definition but only some of them and they are the same considered APS. So there should be also something else that make an application an APS.
I think that a definition should
stress also on ‘how’ the system operates to help planning. And the main features are:
- great speed of computation (achieved by advanced mathematical algorithms but also, often, by means of in-memory dbms)
- powerful visualisation features to let the planner analyze data more easily
- good tools for system integration to fasten the collection of data that can be meaningful for production planning and scheduling.
The main reason the originated APS was that MRP procedure on transactional systems where too slow to let frequent replanning. After
this constraint has been reduced, the visualisation and data navigation features prevent the planner from being the new bottleneck
of the planning process. Data integration is another important aspect that let the planner not to waste time to retrieve data
which are useful for the planning sessions.
Comments are closed.